#DriverlessEd aims to teach consumers about autonomous vehicles (AVs), everything from the driverless technology that powers them, to the rigorous safety practices and the rider experience.
Be sure to explore the previous four chapters:
Chapter 1: Why Driverless Vehicles?
Chapter 2: The Difference Between AVs and ADAS
The rules of the road say drivers should visually inspect the condition of their vehicles every day before getting in and driving off. Are the windshields clear of dirt, debris, ice, or other obstructions? Are the tires properly inflated? Windshield wipers in good condition?
Not all of us follow this best practice, however. Anyone who lives in a cold-weather state may recall a time they saw a vehicle still covered in snow driving down the road.
The National Highway Transportation Safety Administration estimates that 44,000 accidents every year are caused by faulty vehicle equipment. Improperly inflated or worn-out tires alone accounted for 35 percent of these incidents, resulting in hundreds of preventable deaths.
Nothing is more important when operating a robotaxi than safety. This includes the safety of the passenger inside the vehicle as well as all other road users.
It’s why every Motional robotaxi undergoes a thorough, back-to-front, top-to-bottom inspection process every day – a process far more thorough than what’s done by the safest human drivers – before the vehicles are dispatched out onto public roadways.
“Before an airplane takes off, the pilot always walks around the plane, and goes down a checklist, in order to help keep passengers safe,” said Zeb Dawson, Motional’s Senior Director of Commercial Operations. “We do the same thing, even if we drove the car in the morning and are now going out in the afternoon.”
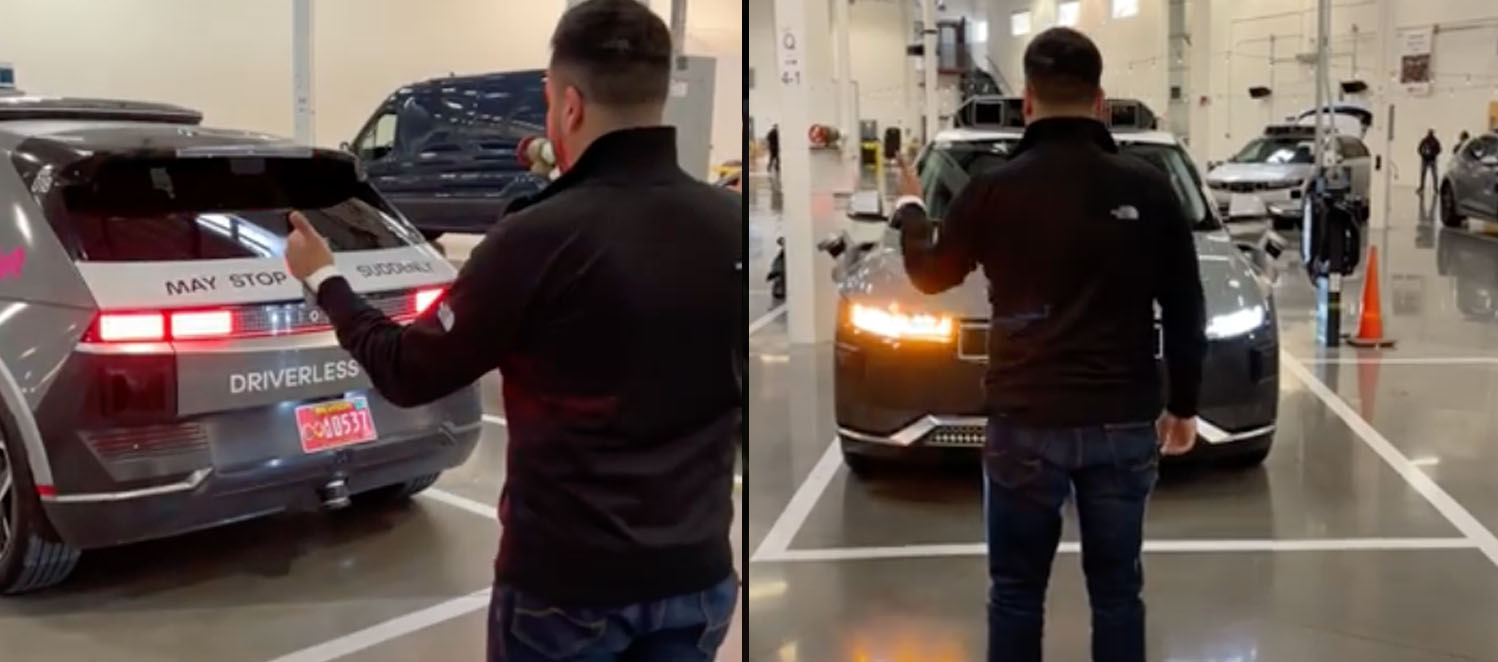
A Motional vehicle technician confirms the blinkers on an IONIQ 5 robotaxi are properly functioning. It's one of multiple safety checks every robotaxi undergoes before starting autonomous operations on a public roadway.
Inspecting the Vehicle
The process starts hours before the first ride-hail passenger requests a ride.
Overnight, the interiors of the robotaxis are thoroughly cleaned. (They might get another refresh if there’s been a mid-shift spill or other incident.) Motional’s robotaxis, which are all fully electric Hyundai IONIQ 5s, also receive a battery recharge.
As the garage springs to life in the morning, every robotaxi scheduled for operation undergoes a 16-step visual inspection. The results of each step are logged electronically.
“We want to make sure we send the car out in good working order, that there’s nothing wrong with it, and we can feel good about putting passengers in the backseat,” said Cody White, Motional’s Commercial Fleet Manager.
Fleet operators go over every part of the vehicle. They make sure each blinker, headlight and taillight works, that the windshield wipers are in good condition, fluid levels are appropriate, brakes are engaging, and so on. They make sure warning lights haven’t popped on overnight and that sensors, a mix of cameras, radar and lidar, are working properly.
Weather can also impact daily preparations. Motional is currently operating passenger service in Las Vegas, which means daytime heat is often a factor. On hot days, team members will check the cabin temperature and make sure it’s cool.
Booting It Up
Autonomous driving is made possible by a suite of sensors and other hardware – cameras, lidars, radars, microphones, antennas, GPS trackers – that works hand-in-glove with onboard computers running highly advanced, machine learning-based driving programs. All of this hardware and software also needs to be checked daily to ensure safety.
Sarah Ishman, a Principal Product Manager with Motional, said just like someone might start up their laptop every morning, the vehicle’s onboard computer needs to be booted up daily. Motional workers follow a checklist to make sure the onboard computer is working properly. They make sure the latest software version is loaded up and properly configured, that all the sensors are working and collecting data, and all the different systems are talking with each other.
Unlike with the visual inspection, much of this work can be done online. Each vehicle is connected to Motional’s command center, allowing team members to check the vehicle’s systems and monitor performance in real time.
From the command center, employees can tell if a vehicle is online and connected, whether its battery is fully charged, if there are any sensor errors, that the vehicle’s antennas are sending and receiving signals, and that it’s connected to the ride-hail network.
AVs use a combination of onboard maps and GPS to understand where they are. One final step is called localization, where the team checks that the vehicle knows exactly where it is.
“It has to be really precise,” said Ishman.
From the command center, the team can also inform the fleet of new road closures, or highlight trouble spots to avoid so that passengers are not stuck in unnecessary congestion.
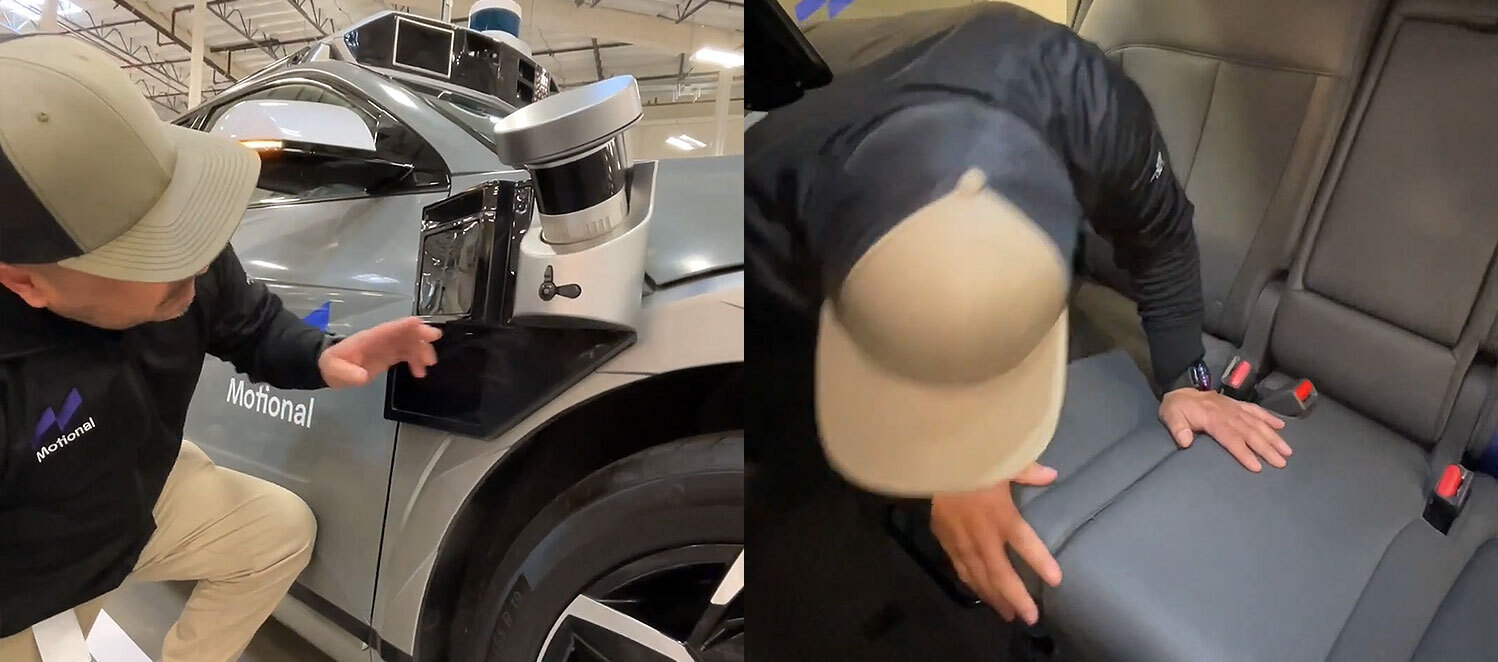
A Motional vehicle technician closely looks at a sensor on the side of an IONIQ 5 robotaxi and inspects the interior of an IONIQ 5 robotaxi.
Ready To Roll
A robotaxi must pass these checks every time it leaves the garage; even if it had already been inspected earlier in the day.
“This process is in place so that every time we go out, we know the lights are working, there are no issues with the tires, that everything is good,” said White. “When there’s no human operator in the vehicle, it’s even more important to have all these checks in place.”
After the robotaxi has passed its visual inspection, and the command center can confirm all the sensors and onboard computers are working, and vehicle localization is confirmed, only then will it ping our ride-hail partners Lyft and Uber that it’s ready for duty.
And when a ride-hail passenger summons a vehicle, they know they can expect a clean, safe robotaxi to pull up in front of them.